An epoxy composite is simply an epoxy resin which has other stuff mixed or laid into it before it hardens. The most familiar composite material made with epoxy is carbon fiber. Though we call the end product a ‘carbon fiber’ item it is more technically a ‘carbon fiber reinforced polymer’ item with the polymer in this case referring to the epoxy resin. Parts made this way are very light for the strength they offer but are expensive.
Reinforcements for polymers are typically cut fiber strands or whole fabric sheets. These relatively large reinforcements are typically ‘laid up’ into a mold and then saturated with resin. I wanted to use other less conventional (and less expensive) materials with epoxy resin as a filler to see what I could create with a specific focus on castable materials. A castable resin mix would need a viscosity low enough to run into and fill the parts of the mold. In addition the filler material would need to address some of the thermal problems encountered when creating thicker parts in epoxy.
As epoxy cures it releases heat. The hotter the epoxy is the faster it cures. These two aspects of thermosetting polymers (including epoxy) limit the thickness which can be cast. If the part is too thick it will not be able to dissipate the heat generated during the curing process resulting in a thermal runaway. In a thermal runaway the heat from curing speeds the curing generating more heat causing a rapid spike in the temperature of the curing resin. The addition of a filler will increase the volume of the epoxy and function as a heat sink to regulate the speed of the reaction.
 |
Aluminium Filler Epoxy Composite |
Samples created for this experiment were of two sizes. The smaller is approximately 40mL in volume while the larger (such as the above pictured) are approximately 90mL in volume. This first sample is about 50% aluminum powder by volume. When working with fillers it is important to consider how much space the filler will consume as compared to the resin. Since it is troublesome to measure these materials by volume their densities are consulted and the mass to be mixed in is determined which allows the appropriate amount to be scaled out.
Reducing resin volume to less than 60% when using aluminum as a filler significantly increases the viscosity of the mixture making it both more difficult to mix as well as pour.
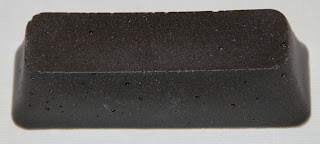 |
Iron Filing Epoxy Composite |
This 90mL sample is 30% iron filings. The iron filings using in this sample came from a set intended for science demonstrations and as such are not particularly fine or cheap. I found sources of powdered iron on ebay later but not in time for this first batch of samples. Air pockets are clearly visible throughout the sample. While none of the samples examined here were vacuumed after mixing the effects of air entrainment are most visible on this sample.
Because of the iron present this sample has ferromagnetic properties though the resin’s presence greatly diminishes them.
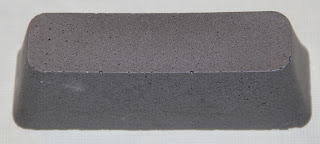 |
Iron – Aluminium Epoxy Composite |
This 90mL sample is 20% aluminum, 30% iron. The addition of the aluminum seemed to decrease the viscosity of the resultant mix compared to the previous iron sample. Otherwise it is exactly what one would expect compared to the previous iron or aluminum only samples.
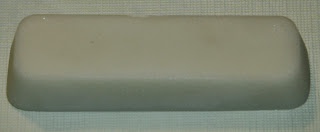 |
Marble Powder Epoxy Composite |
This 40mL sample is the first of the marble powder samples. Powdered marble makes up 40% of the volume of all the marble samples. All individuals presented with these samples determine them to be some type of stone with a minority guessing them to be marble. None supposed them to be a composite.
After this experiment I discovered cultured marble used in bathroom vanities and many other solid surface countertops are created using a similar process. These samples are different in their use of an epoxy resin as compared to the more conventional polyester resins used in commercial products.
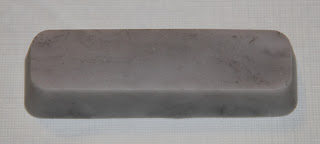 |
Marble Powder Epoxy Composite – Black Colorant |
This sample had a black ink added after the mixing of the resin with the marble powder. The contrast is more pronounced in other samples. It is key the colorant not be added until after the resin has been completely mixed. Excessive mixing of the ink into the resin would create a uniform distribution of the colorant removing the striated effect seen.
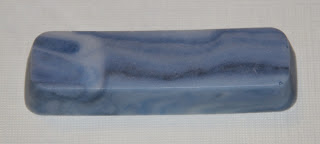 |
Marble Powder Epoxy Composite – Blue and Black Colorant |
Blue and black colorants were used in this sample. Various effects are possible via the manner in which the colorant is added and mixed into the resin as well as how it is poured into its mould.
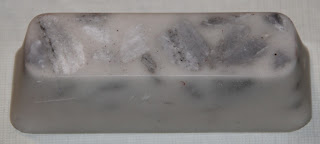 |
Powdered Marble / Marble Chip Epoxy Composite |
This sample was filled with both marble powder and whole pieces of marble in ratios similar to those used for course and fine aggregates in concrete. Both items (the epoxy sample and concrete) are similar as they are both composites of a large aggregate (to take up most of the volume), a fine aggregate (to fill the smaller spaces), and a binder to hold everything together (cement in the case of concrete and epoxy in the case of the sample). The red spots on the sample are the uncleaned remnants of the polishing compound used to polish the marble chips. The marble powder and resin matrix does not seem to respond well to polishing compound though it can be sanded to a relatively fine grit.
For a comparison of how a ‘clear’ resin (one without reinforcements or modifiers) cures compared to a resin with filler consider the following. The 90mL samples discussed above are just over an inch in depth and did not exceed 80F during their curing process. A 90mL block of clear resin cast into the same mould as the above samples exceeded 240F during its curing process. The high temperature experienced during curing caused the piece to deform in its mould. This might be correctable with a rigid mould (the mould used for these samples was a flexible silicon cookie bar mould) but this would likely lead to problematic stresses in the sample.
In conclusion these fillers seem to be capable of allowing epoxy to be used to cast larger parts than normally possible with clear resin. General appearance seems to be highly mutable based on added colorants and fillers. Further tests will be necessary to determine the machinability and general strength of these samples.